
A lot of types of facilities critically depend on ventilation: e. g. drug laboratories or laboratories that work with volatile substances. Failure to provide certain temperature, humidity, and airing might lead to their deterioration or unsafe work conditions.
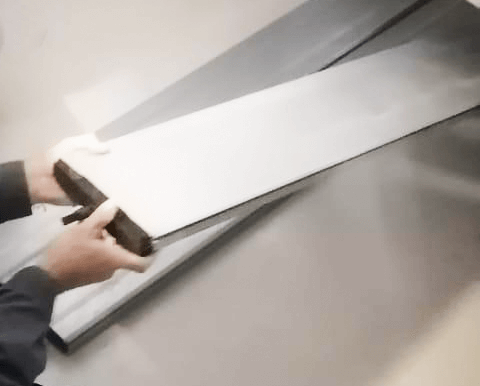
Air conduct blades are large metal stripes that control the air flow inside ventilation systems. On sides, these blades are held by plastic components connected to their drive within a plastic casing.
That plastic — originally glass filled PA — is not durable enough to operate under high bending loads caused by strong airflows. When it eventually breaks, there is no other option than to buy the whole electric component as they are not designed for maintenance. In our case, the component price is € 285.
Creating reliable spare parts on demand with continuous fibers
The parts, engine cases and air blade holders, were adjusted by our team in Aura for 3D printed composite materials: truss plates were removed; in order to reinforce walls as much as possible they were made thicker, also, we adjusted the printing profile and sacrificed the smooth surface finish for better durability.
The parts were printed with Smooth PA and reinforced with several perimeters of Composite Carbon Fiber (CCF). For the model below, the inner plastic perimeters were removed, leaving only 2 external plastic layers and one fiber perimeter. In order to fit in the fiber, the path width was reduced from 0.75mm to 0.5mm. The plastic path width — from 0,4mm to 0,3mm

Reducing the path width while keeping the standard line height can create excessive pressure in the chamber and lead to fiber clogging during the printing process. In order to prevent it, the printing height was increased from 0.08mm to 0.1mm for plastic and from 0.35mm to 0.45mm for the fiber.

Successful spare part management with continuous carbon fiber 3D printing
Most businesses are reluctant to maintain an adequate spare parts inventory as they believe storing spare parts is counterintuitive to managing costs. Composite 3D printing helps to reduce costs and maintain efficiency: The printed spare parts not only save the cost and increase service intervals, but are also designed to withstand more load and be more robust.

Material | Drive case | Blind | Fixture |
---|---|---|---|
Weight, g | 46 | 52 | 24,3 |
Cost, € | 21.6 | 14,5 | 12 |
- The result is now more sustainable use of resources and substantial savings: €24 instead of €285
- The indirect benefits include longer maintenance intervals and more reliable operation, thus labor safety and responsible storage

WANT TO STAR PRODUCING LIGHTWEIGHT COMPOSITE SPARE PARTS ON YOUR DEMAND? GET IN TOUCH WITH OUR TEAM:
[hubspot type=”form” portal=”25897477″ id=”74952842-0877-4fd8-9c76-a728c5860746″]