
Why treating composites like isotropic materials is not a a good idea
So the following approach was adopted: engineers create a quasi-isotropic composite and then treat it like isotropic material. They layer stripes and fibers and cloths in all the directions so that they resemble isotropic material, and then apply the same methods as for metals.
But it basically kills all the advantages of composites, here are the values for both aluminum and Continuous Fiber Reinforced Polymer.
Material | Strength | Density |
---|---|---|
Aluminum | 400 MPa | 2.7 grams\cm3 |
CFRP | 2 GPa | 1.7 grams\cm3 |
It means that you can build structures that are ten times stronger, but in one direction. The strength of laminate, a quasi isotropic composite, is only 300, which is less than that of aluminum. Yes, it is still lighter, but the trade-off is only a 20-30% increase in strength rather than a tenfold increase.
Then there are the cracks, delaminations, barely visible damage, poor impact resistance, monitoring, maintenance, costs, and so on. Finally, a 20-30% bonus does not compensate for all of the problems you encounter.
People in the industry are pessimistic about composites because they believe that quasi-isotropic design is the only way to create composites, which is not true.
Understanding the benefits of Anisotropy – the key to design optimal composites
Before we started our company, I focused my scientific work on simulations and the optimization of composite materials and discovered that it is much more logical to utilize the directional properties of composites in the design process, and that is when magic happens.
Mathematically speaking, when a structure is loaded, there is a response called stress at every point where the load is applied. And stress is a directional value; it is not a vector, but a tensor, which is more complex, but it is directional nonetheless.
The tensor has a principle: for each material point, there is an internal resistance that has a direction; consequently, material properties should be concentrated along this direction. You only require material properties along the direction in which the material resists. And you do not require them in other directions, or only to the extent that the material resists in this direction.
For isotropic material, the stress resistance pattern is spherical and uniform in all directions. However, your material strength only resists in one direction; the rest directions are redundant.
Thus controlling anisotropy in every material point — both orientation and the ratio allows to design a structure that would fit exactly the response. In a conventional design paradigm there is still optimization, but only the shape.
Composites allow optimization of the shape, internal structure, and properties – so it is another optimization dimension. With this dimension, it is possible to create much more optimal structures where the material works exactly in the required directions and points. But that’s not the way it is done in industry today.

Generative design - How nature uses composites
We worked on topology optimization and generative design of anisotropic media and the results looked completely different and more natural.
And this is quite obvious because generative design and evolution share a similar methodology. Not identical, but it is comparable. Thus, it is evident that we obtain comparable results.
This is when I pondered, what if you examine nature to determine what natural materials exist? What are the natural evolutionary design materials, how do they look?
The examples are everywhere in nature: trees and grass contain fibrous materials. Even the human body has fibers (collagen): in muscle and skin. The method is omnipresent in nature, it means that it is energy efficient, which is the most important thing for the evolution. And one last funny thing: nature did find a way to use metals as building materials. So there are metals in the environment here and there, but nature hasn’t found a way to use them to build structures because it would waste too much energy.
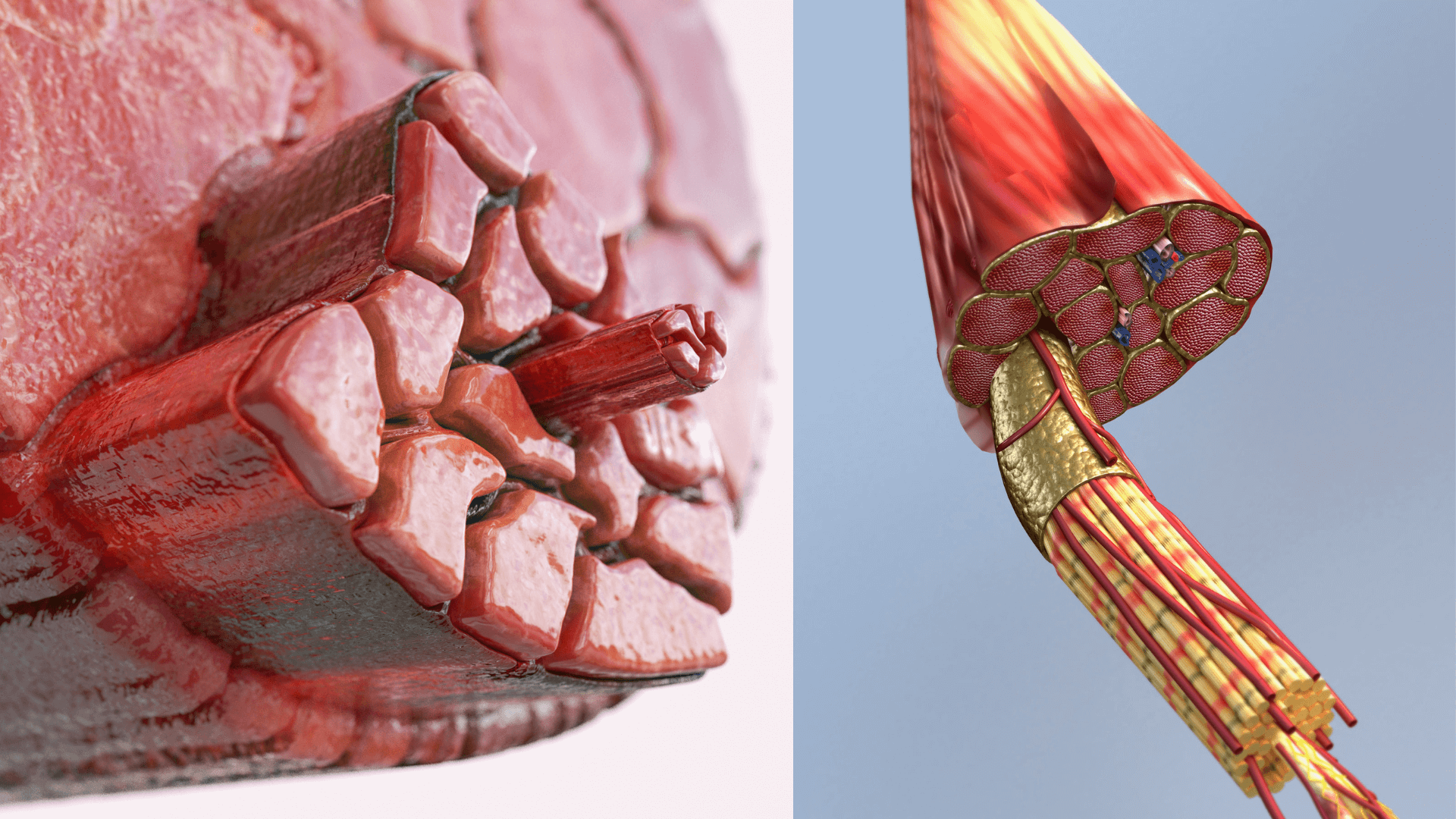
Building metal-free constructions with fiber reinforced composites
To make something out of metals, you need a lot of energy to process them. It means that it is not optimal and it is gonna be obsolete, so we won’t be using metals in the future as obviously there will be composites or fiber reinforced composites. There is already a tendency to replace metals with composites in construction:
So the way nature does evolution is actually a bit different from the way we do or can do optimization. And this is funny, because nature does it adaptively. Each palm tree has its DNA so it knows how to build itself, but then it builds itself under changing environments and it adapts. And these are very interesting things.

There are a few instances in which humans employ this strategy, but in general, we envision an environment, describe it, and then say, “Our structure should work in this environment.” We then build the structure, place it in the environment, but it is not adaptively grown. That’s probably too futuristic, but in the future we’ll likely discover how to manufacture adoptive structures, and then we’ll take the next step.
The design process of composites may seem daunting at first, with a little effort it is possible to create structures that are much more efficient and effective. We can help you rethink your product design using composites.
Are you ready to start exploring? Fill out the form below:
[hubspot type=”form” portal=”25897477″ id=”74952842-0877-4fd8-9c76-a728c5860746″]