
Types of prepregs: different materials and forms
In a more broad sense, prepregs are reinforcing fibers soaked with matrix polymers: fibers can take the form of a thread, tape, or fabric and can be made of different materials, commonly glass, carbon, basalt, kevlar, etc.
The matrix can be thermoplastic (PE, nylon, PPS, PEEK, PEKK, PEI) or thermoset (epoxy, phenolic). The abundance of fiber-matrix combinations results in a wide range of properties.
Thermoset prepregs
They are made by impregnating a fiber reinforcement with a liquid thermoset resin. The term “thermoset” refers to the type of polymer that hardens or “sets” with the help of a curing agent when heated to a certain temperature and cannot be remelted or reshaped.
The thermoset resin curing process has three stages:
— A-stage: Mixing the resin with a curing agent (without chemical reaction).
— B-stage: The chemical reaction has started: viscosity and tackiness of the mixture are increasing.
— C-stage: The resin has fully cured after catalyzing in an autoclave.
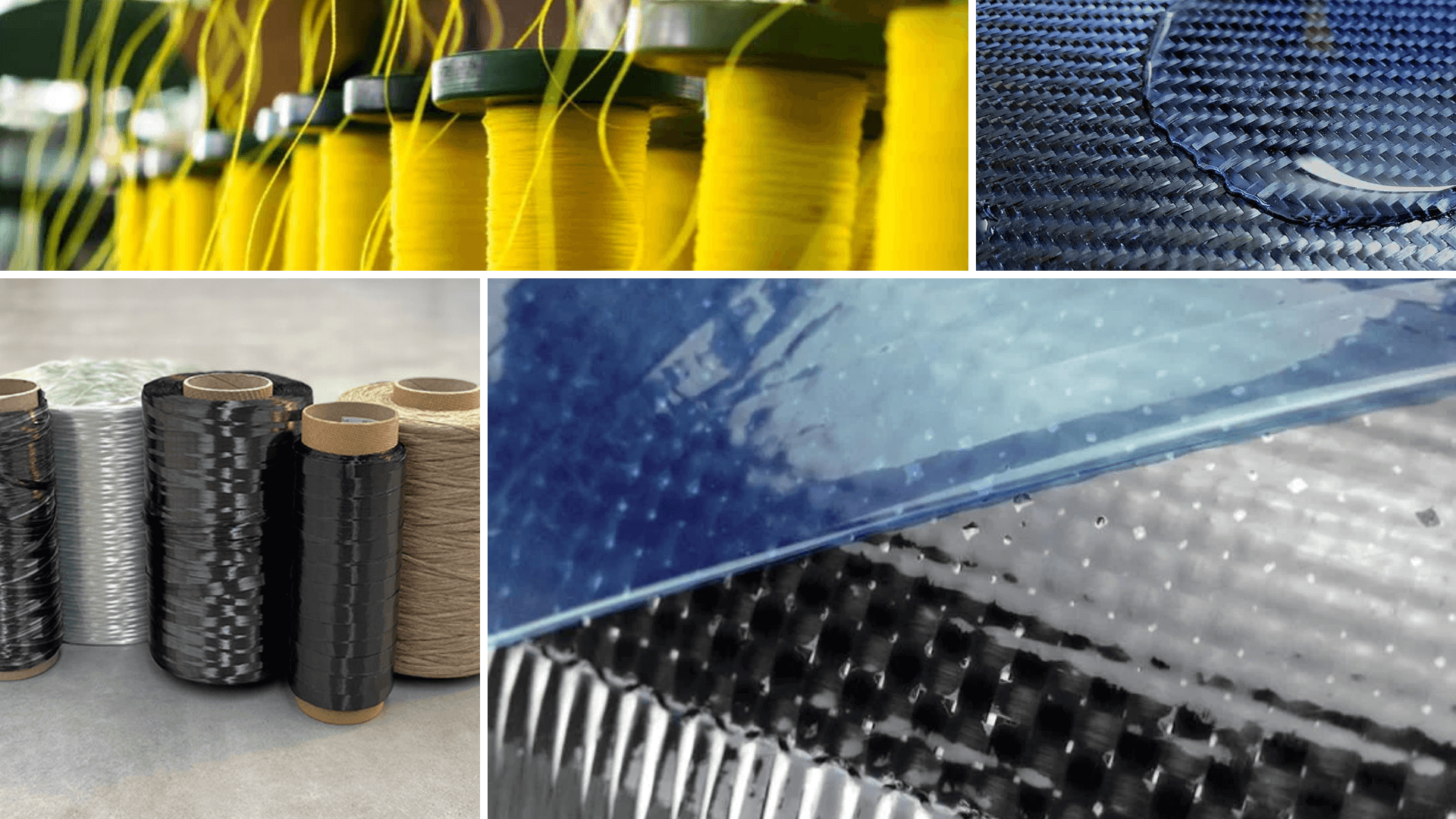
Once the fibers are impregnated with the thermoset resin, the prepreg is rolled and stored at a controlled temperature and humidity until it is ready to be used in the manufacturing process. The prepreg is then cut to the desired shape and placed into a mold. As the epoxy is in the B-stage, it must be stored either refrigerated or frozen before usage. Otherwise, the total shelf life is typically under 8 weeks.
The most common thermoset resins used in prepregs are epoxy and polyester. Epoxy is a versatile and widely used resin that offers excellent mechanical properties and chemical resistance. Polyester thermoset resins, on the other hand, are less expensive and offer good resistance to impact and abrasion, but have lower mechanical properties compared to epoxy.
Thermoset prepregs are widely used in aerospace, automotive, and wind energy industries. They are known for their high strength-to-weight ratio, excellent fatigue resistance, and are widely used in the production of high-performance composite structures such as aircraft parts, racing car parts, and wind turbine blades.
Thermoplastic prepregs
These are made by impregnating a fiber reinforcement with a thermoplastic resin, such as polyethylene or polypropylene. The resin is heated to a specific temperature and then cooled to create a solid composite material.
By contrast with thermoset, thermoplastic prepregs are pre-impregnated with thermoplastics (can be melted several times).
 — Low-temperature: PP, PET, PE, PA, PPS.
Polyethylene and polypropylene have good chemical resistance and low density, making them suitable for applications requiring weight savings. Polyamide, commonly known as Nylon, is known for its toughness, high abrasion resistance, and good fatigue resistance.Â
 — High-temperature: PEEK, PEKK, PEI.
Thermoplastic prepregs have some advantages over thermoset prepregs, such as the ability to be reheated and reshaped multiple times, increased environmental resistance and improved impact resistance. Also, thermoplastic prepregs are stable at room temperature, and generally, do not have a shelf life, however, due to greater viscosity of thermoplastic it is harder to manufacture them: liquid thermoset quickly soaks fibers without leaving bubbles, and thermoplastic is tacky and does does not soak the fibers so easily.
Towpreg tapes and Composite Carbon and Basalt Fiber (CCF)
There are other composites that are made of fibers impregnated with either thermoset (most commonly) or thermoplastic, they feature continuous fibers and are wound onto a spool for easy handling and storage.
Towpreg tapes – from 3 to 300mm wide – are used in AFP and ATL technologies that are aimed at 3D printing simplistic flat shapes and fast production. Here, the narrower the tape, the more freedom it gives in shape complexity.
At Anisoprint, we use pre-impregnated carbon and basalt fiber threads that allow to 3D print continuous fiber reinforced components with highly complex shapes.

“Prepregs are broadly defined as impregnated, but uncured sheets for subsequent molding and curing, and are in stage B, that is, semi-cured. And they have a shelf life and should be stored in a refrigerator. We use fully cured fiber, which is not a prepreg in the traditional sense, but a towpreg that has been cured almost entirely, already at stage C. However, the fiber softens during the printing process and can be shaped.” — Alexander Kochetkov, Anisoprint's Head of R&D.
Thermoset impregnation allows to keep the fiber share as high as 60% of the total volume. Such continuous carbon fiber allows to print anisotropic composites that exhibit excellent strength to weight ratio.
Advantages and limitations of prepregs vs hand laminating
There are a number of advantages of prepregs compared to hand laminating (manually applying the matrix to dry reinforcing fabric). Â
 — Maximum strength: the optimal ratio between the fiber and the matrix is 50/50. It is quite hard to achieve in hand laminating where we run the risk of having too much excess resin and thus increasing brittleness. As most prepregs contain 35% of resin, this becomes much easier when one does not have to control the volume by sight.
 — Naturally, preliminarily impregnated materials save a lot of effort, that is why they were invented. Prepregs do not require a separate facility with equipment for dripping resin, that is not to mention that most curing agents are hazardous and you do not want to handle them on your own and run the risk of the epoxy curing too fast.
 — Also, compared with hand lamination, prepregs require less curing time, which is important for commercial applications.
 — Last but not least, parts from prepregs feature excellent surface due to easy molding and allow good repeatability and uniformity.
However, good things do not come for free, and inconveniently, prepregs are quite cost prohibitive:Â
 — Prepregs cost more than the resin, cure, and fabric together.
 — The warmer the place, the less is the shelf life of a thermoset prepreg, though freezing should help to keep the material usable.
 — Finally, all technologies involving prepregs are associated with autoclaves or vacuum bags for curing the material, which implies additional power and equipment costs.
Curious to learn about composite carbon fiber? Ask our experts:
[hubspot type=”form” portal=”25897477″ id=”24e694d6-414d-4083-8bc0-e73890c8a8f3″]