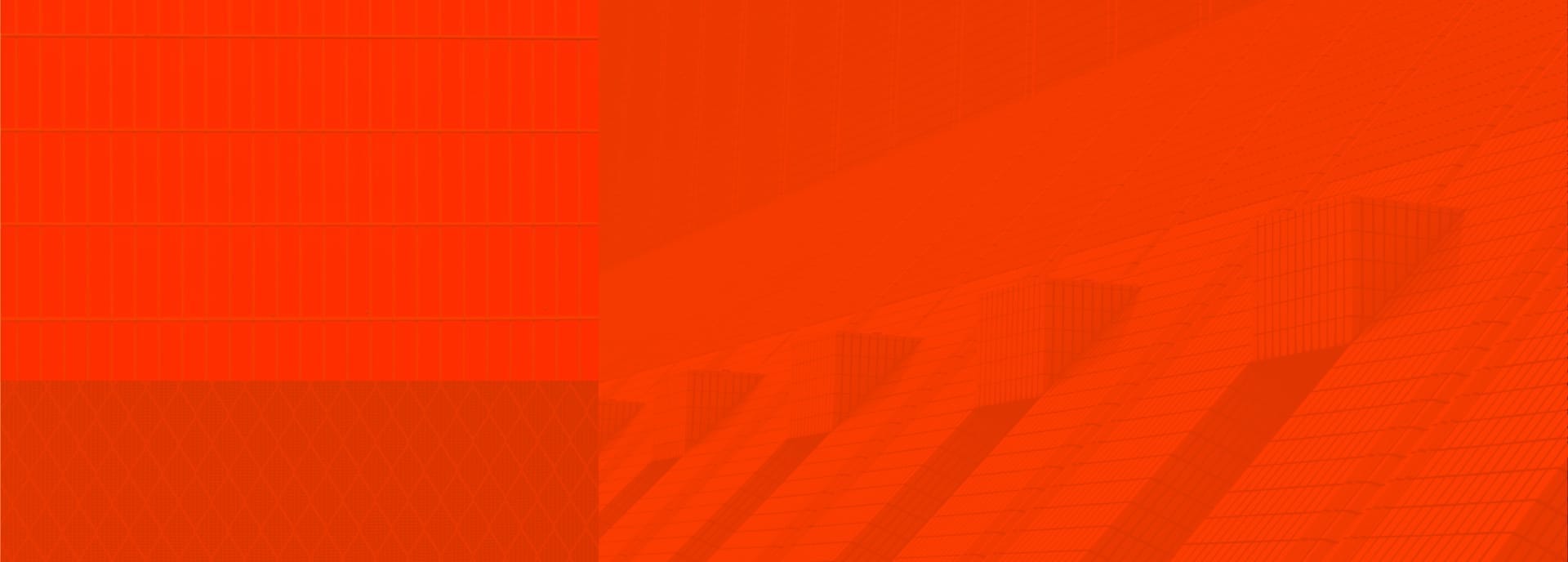
Stop metal thinking
start anisoprinting
- Custom trajectories of fiber laying
- Freedom in materials choice: any plastic as a matrix
- Open G-code
- Non-cloud software
- Printing lattice structures: the most optimal shape for composites
- Getting maximum strength spending minimum material
- 30 times stronger than plastic
- 7 times lighter than steel
- 2 times stronger and lighter than aluminum

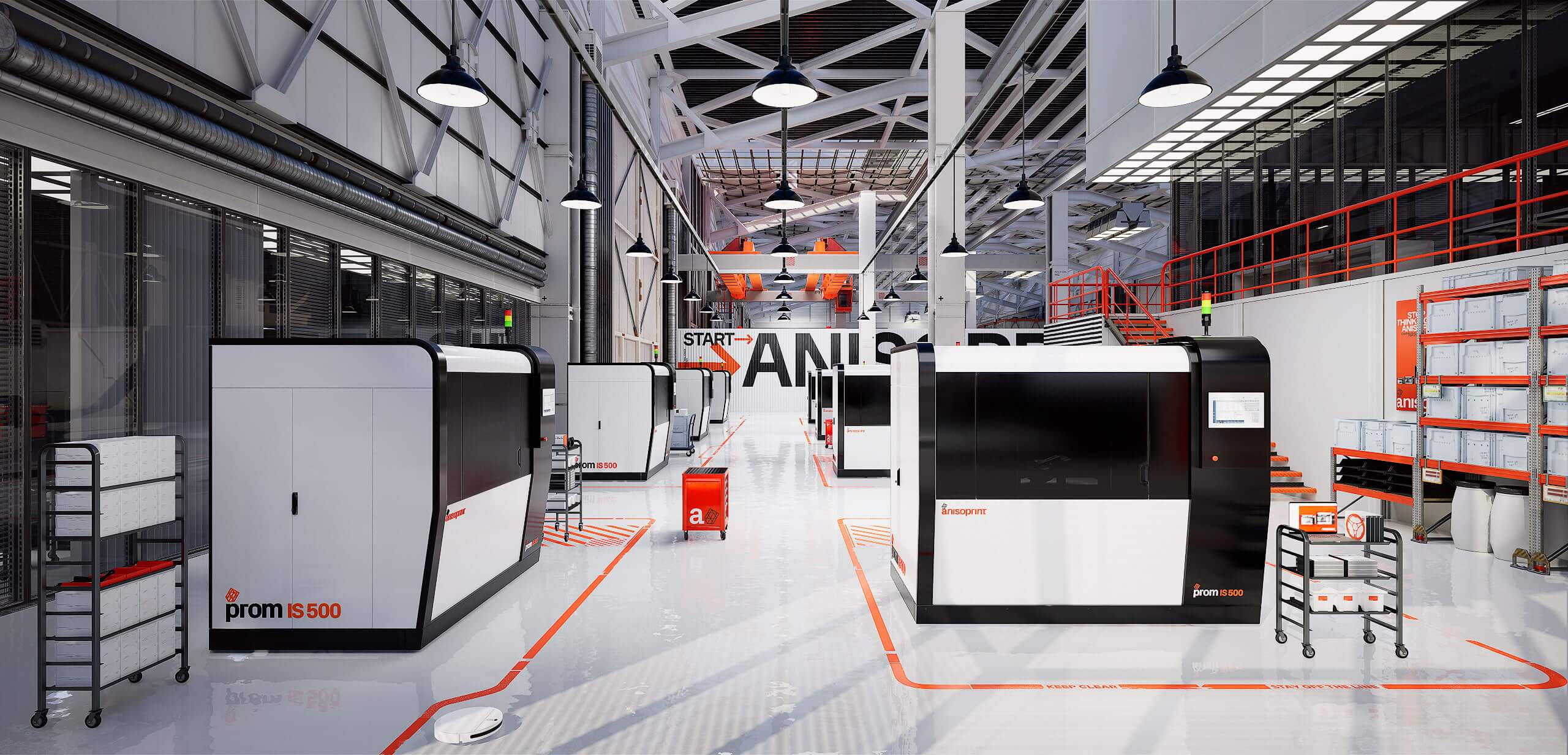
is in anisoprinted composites
Composite materials have a heterogeneous internal structure, as a result, they are extensively used in the aerospace, automotive and civil engineering sectors. The main characteristic of such materials is the presence of two different phases: matrix, or binder, and reinforcement. The reinforcement resists the main loads, while the matrix makes the individual reinforcement elements work together. In structural composites, high-strength fibers such as carbon, glass or organic are used as the reinforcement element, providing significantly higher specific strength and stiffness compared with any metal.
Matrices are predominantly polymers, although composites based on metallic, ceramic and other types of binders are widely known. The main feature of such fibrous composites is their anisotropic properties. That is, the material response to external loads depends significantly on the direction of these loads. For example, the cCFRP ((continuous) carbon fiber reinforced polymer) strength differs by two orders of magnitude depending on whether the load is applied along the direction of the fibers, or transversely. Traditionally, this feature of composite materials is considered to be one of their main disadvantages, limiting their mass use in most industries. The anisotropy is hardly repulsed, mainly by making so-called quasi-isotropic laminates – or sheet materials – in which the layers of a unidirectional composite are stacked at different angles. This results in material behaviour comparable with metal sheet in a plane stress state. Furthermore, with the exception of the moulding step, they are often used in exactly the same way: cut, drilled, connected with rivets and bolts, which destroys the integrity of the reinforcing fibers, which in turn leads to additional stress concentrations due to the free edge effect and other features inherent in composite materials that reduce the overall strength of the structure.
This is where nature can point us in the right direction: wood fibers do not break off at the point where the branches grow, but gently warp around, compacting locally. Fibers in the leaves form a complex branched structure of reinforcing ribs, not forming an edge to edge on top of each other in several directions, breaking off at the ends. The internal forces, or stresses, that arise in these bodies as a reaction to external loads, have a tensor nature, that is, at each point, there is a distribution of stress values relative to three spatial directions. The material response at each point is non-uniform, and therefore, the material must also be non-homogeneous to optimally “work off” this response.
A classical isotropic material must be able to withstand the maximum stresses at a given point in a certain direction. In this case, the stresses in the remaining directions can be much smaller, but the strength of the material in these directions is the same, which means that it is redundant. Anisotropic material should allow the properties to be optimized, providing the minimum necessary characteristics in different directions. The simplest example is the rod, that works just in tension along its axis. In this case, all the fibers must be parallel to this axis, and the transverse properties of the material do not matter. Such a rod is the most effective composite part.
Based on these considerations, the most efficient composite design is a structure that consists of a set of rods connected to each other in such a way that each rod perceives only the load along its axis. This is a so-called lattice structure. It is not surprising that most topology optimized structures are lattice structures.
In this sense, we would suggest that the use of composite materials is the best option for making such optimized designs. It should also be noted that such designs are successfully used in the production of rocket and satellite composite structures, but the technological features associated with the process of manufacturing such structures impose significant restrictions on their shape, as well as the relative alignment and choice of the direction of the ribs.
Here, at the intersection of composite materials and additive technologies, a fundamentally different industrial approach. Real 3D, not only by shape but by internal structure. If you factor in the potential capability to incorporate sensors and transducers, through functional fibers, the option to create adaptive designs by building electronics and special functional components directly into the material during the original production process emerges. Furthermore, this introduces the potential to create smart and self-healing materials and 3D structures in-situ by inserting special components while printing or arranging the delivery of healing agents through dedicated channels inside the material.
The process itself now ceases to be layer-by-layer, because the direction in which the reinforcing and functional fibers are laid is of fundamental importance. All of these possibilities are unattainable within the framework of a layer-by-layer paradigm of additive manufacturing. In practice, such equipment can be implemented on the basis of fiber-polymer co-extrusion or automated fiber placement. A print head containing extrusion nozzles through which reinforcing or functional fibers and a polymer resin are fed is mounted on a multi-axis manipulator that performs the positioning of the head arbitrarily in space with respect to the part being built.
The part itself can also be placed on the robot or on the bed. The entire process takes place in an enclosed, thermo-regulated chamber to ensure adhesion between the fiber bundles and to eliminate the shrinkage and warpage effects. The volume fiber volume fraction can be locally varied by means of a separate feed for the reinforcing fiber and resin, while the manipulator must ensure the layup along complex, curvilinear, spatial trajectories. In this way, it is possible to control the degree of anisotropy at each point, ensuring the production of optimal structures of complex shape and internal structure. Additional positioning devices can incorporate electronic and other functional components into the part.
The real future of additive technologies is in composite materials with controlled anisotropy, shape and internal structure optimization-based design, multifunctional capabilities and adaptive structures. To get ahead now, it is necessary to use additive technologies at a new level — a composite level.
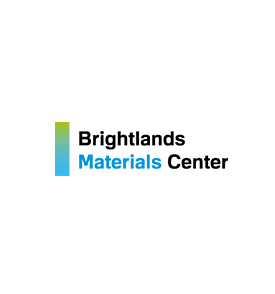
Anisoprint members have been extremely helpful and available to solve all our problems with the printer since the first day. We are very satisfied by the service".
— ANDREA GASPERINI, Project leader, Brightlands Materials Center
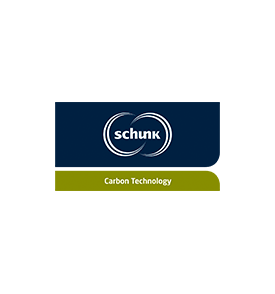
— GOTTHARD NAUDITT, R&D Engineer Composites, Schunk Carbon Technology
It is a milestone in the path of Jacobs University in its ambition to become one of the Top 15 global young universities with a focus in key areas such as Data Science for Business, Quantum Computing and Technologies, Advanced Materials, and Modeling of Complex Systems. Additionally to the educational benefits, it brings great value to the whole economic area of Bremen.