Prepregs, or preliminarily impregnated fibers, are typically reinforcing fabrics pre-impregnated with a resin system (thermoset or thermoplastic). These flexible sheets are laid up in a mold for getting the right shape and require no additional materials, they are commonly used for the manufacturing of advanced composite structures.
What are prepregs?
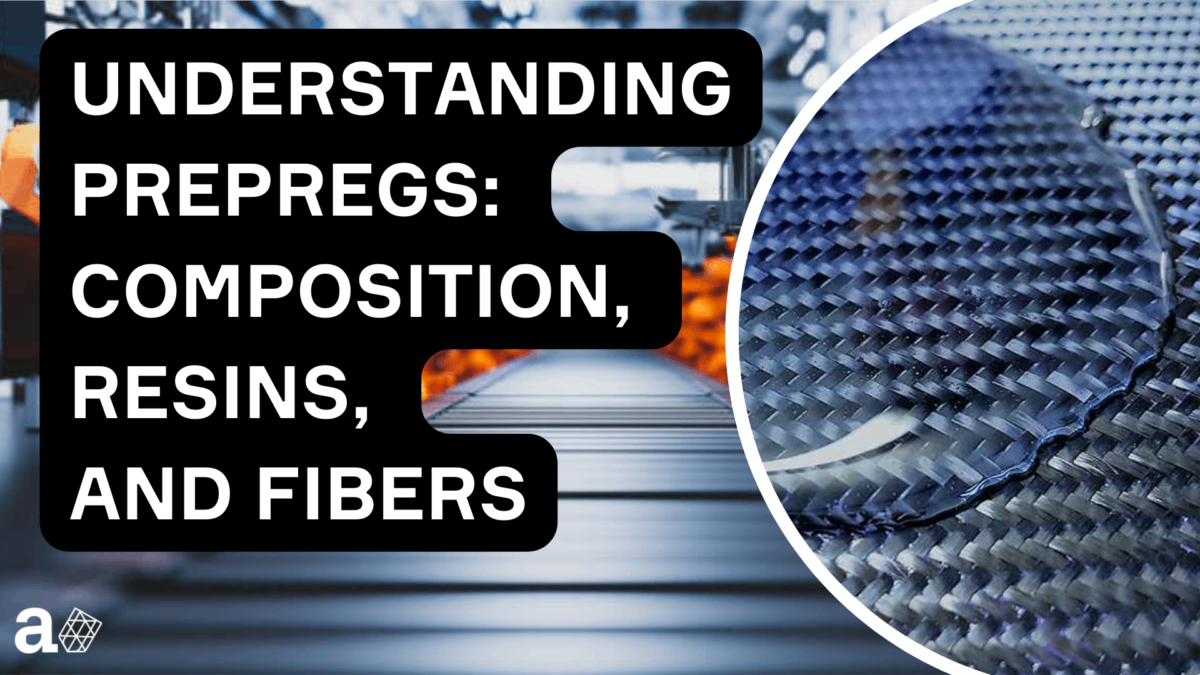